
HOUSE
A resilient landscape is fire-wise, water wise and promotes biodiversity by using California native plants. These gardens use sustainable practices, plant selection, and maintenance to reduce the risk of fire in the defensible space zone. Resilient gardens save water, protect us from fire and promote biodiversity.
NEW
Roof
The roof is the most vulnerable component of your home! During a wildfire it must be able to resist wind-blown embers and other wildfire exposures. Complex roofs, where the roof meets vertical walls and/or includes dormers, present additional vulnerabilities. Replacing a roof is a major project, but it can yield major benefits. Evaluating the vulnerability of the roof should be a top priority when considering a new home or remodeling an existing property. Proper roof maintenance is critical to reduce the ignition risk of your home!
RELATIVE COST AND PRIORITY LEVEL OF HOME HARDENING FEATURES FOR FIRE-RESISTANCE
![]() |
![]() |
![]() |
![]() |
![]() |
![]() |
|
![]() |
||||||
![]() |
![]() |
![]() |
![]() |
|||
![]() |
Relative cost: Indicates the relative cost of upgrading the listed features to ember-resistant materials and design.
Priority level: Indicated the features most vulnerable to wildfires and embers. Keep in mind each situation is unique and may change your priority level.
Roof Covering and Assemblies: Install Class A Roof
Roof covering fire ratings are Class A, B, C, or unrated; with Class A providing the best performance. Common Class A roof coverings include asphalt fiberglass composition shingles, concrete and flat/barrel-shaped tiles. A roof can achieve a Class A rating on its own (stand-alone Class A) or when combined with other fire-resistant elements (assembly-rated Class A). Some materials can have a “by assembly” Class A fire rating. This means that additional materials must be used between the roof covering and sheathing to attain that rating.
1. Stand-alone Class A
Common stand-alone Class A roof coverings include:
- Clay tiles
- Slate
- Asphalt fiberglass composition shingles
- Concrete and flat/barrel-shaped tiles
- Some metal roofing materials
2. Assembly-rated Class A
Some materials have a “by assembly” Class A fire rating which means, additional materials must be used between the roof covering and sheathing to attain that rating. Examples of roof coverings with a “by assembly” fire rating include:
- Aluminum roofs (because of their low melting point)
- Pressure-impregnated fire-retardant treated shake or shingle covering (not allowed in many jurisdictions)
- Some recycled rubber and or plastic composite materials.
Block Gaps between Covering and Sheathing
Some roof types are subject to gaps between roof covering and sheathing which typically occur at the ridge and edge of roofs.
These openings can allow birds and rodents to build nests with materials that are easily ignited by embers. Flames from this type of ignited debris can spread to the structural support members, bypassing the protection offered by a Class A rated roof covering. Plugging these openings between the roof covering and the roof deck, is commonly called “bird stopping”. Regularly inspect and maintain these areas.
Cover Chimney with Screen
Windborne embers and firebrands can enter your home through your chimney or stovepipe outlet if it is not protected and maintained correctly. Vegetation debris can also accumulate on the roof adjacent to the chimney chase. This is another roof-to-wall connection that can be vulnerable to ignition by embers.
- Cover your chimney and stovepipe outlets with noncombustible corrosion corrosion-resistant metal mesh screen (spark arrestor), with 3/8-inch to 1/2-inch openings. Do not use fiberglass or plastic mesh as they can melt or burn.
- Remove tree branches within 10 feet of any chimney outlet.
- Install metal-flashing at roof-to-siding intersection to reduce the vulnerability of the chimney chase.
Check Installation Instruction for Class A rating
It can be difficult to determine if the fire rating of a given product has a stand-alone or assembly-rated rating, since a published Class A rating could refer to either. If you aren’t sure, obtain a copy of the installation instructions for the roofing materials.
If the installation instructions call for Dens-Deck, a Type 72 capsheet material, or other materials in addition to Type 15 or 30 roofing felt and structural sheathing (plywood or oriented strand board), you have an assembly-rated Class A covering.
Wood / Organic Material
Re-roof with materials such as composition, metal or tile (see Class A materials in recommendations for new constructions). An untreated wood shake or shingle roof covering is arguably the greatest threat to a building.
Resources:
Wildfire Research Fact Sheet – Roofing materials (NFPA, 2017)
P-737 Home Builder’s Guide to Construction in Wildfire Zones (FEMA, 2008)
Ready, Set, Go guides and videos (FireSafe Sonoma, 2019)
Home Survival in Wildfire-Prone Areas: Building Materials and Design Considerations (UCANR, 2010)
Homeowner’s Wildfire Mitigation Guide – Roof Covering (UCANR, 2019)
Wildfire Home Retrofit Guide (University of Nevada, Reno Extension, 2020)
Preparing Your Home (University of California Cooperative Extension, 2022)
State Fire Marshal Listed Wildland Urban Interface (WUI) Products Handbook (Cal Fire, 2021)
Gutters
Wind-blown debris (including leaves and pine needles from nearby and overhanging trees) will accumulate on roofs and in gutters. Dry debris can be ignited by wind-blown embers. These flames can extend to the edge of the roof and adjacent siding. Even with Class A fire-rated roof coverings, vertical surfaces next to the roof edge will be exposed to flames from the ignited debris.
RELATIVE COST AND PRIORITY LEVEL OF HOME HARDENING FEATURES FOR FIRE-RESISTANCE
![]() |
![]() |
![]() |
![]() |
![]() |
![]() |
|
![]() |
||||||
![]() |
![]() |
![]() |
![]() |
|||
![]() |
Relative cost: Indicates the relative cost of upgrading the listed features to ember-resistant materials and design.
Priority level: Indicated the features most vulnerable to wildfires and embers. Keep in mind each situation is unique and may change your priority level.
Install Leaf Guard
Install noncombustible leaf guards over gutters to prevent the accumulation of combustible debris. Types of leaf guards include metal-mesh screens and metal hoods that fit into the gutter.
Use Noncombustible Materials
Use gutters and downspouts constructed of noncombustible materials such as galvanized steel, copper, and aluminum. Metal hood leaf guards are recommended because they do not melt and are relatively effective in keeping debris out of gutters.
Install Drip Edge
Some metal gutters have an integral flashing piece that serves the function of a stand-alone drip edge. If a drip edge is not present, install one.
The drip edge will serve two purposes:
- it will help protect the roof edge (sheathing and fascia) from a flaming exposure that could occur if debris is ignited by wind-blown embers, and
- it will minimize the entry of embers into a soffited-eave construction by blocking the small gap that can exist between the edge of the roof sheathing and the top of the fascia.
Sources:
Wildfire Research Fact Sheet – Roofing Materials (NFPA, 2017)
Fact Sheet No. 9 – Gutters and Downspouts (FEMA, 2008)
P-737 Home Builder’s Guide to Construction in Wildfire Zones (FEMA, 2008)
Building and Living in the WUI (VCoFD, 2019)
Home Survival in Wildfire-Prone Areas: Building Materials and Design Considerations (UCANR, 2010)
Vents
Roof vents are important features for air circulation and removing excess moisture in the attic. However, they are highly vulnerable to flame entry and ember attacks. The under-eave area is also vulnerable as embers can get trapped in gaps. Under-eave vents are therefore vulnerable entry points for embers to reach the attic.
RELATIVE COST AND PRIORITY LEVEL OF HOME HARDENING FEATURES FOR FIRE-RESISTANCE
![]() |
![]() |
![]() |
![]() |
![]() |
![]() |
|
![]() |
||||||
![]() |
![]() |
![]() |
![]() |
|||
![]() |
Relative cost: Indicates the relative cost of upgrading the listed features to ember-resistant materials and design.
Priority level: Indicated the features most vulnerable to wildfires and embers. Keep in mind each situation is unique and may change your priority level.
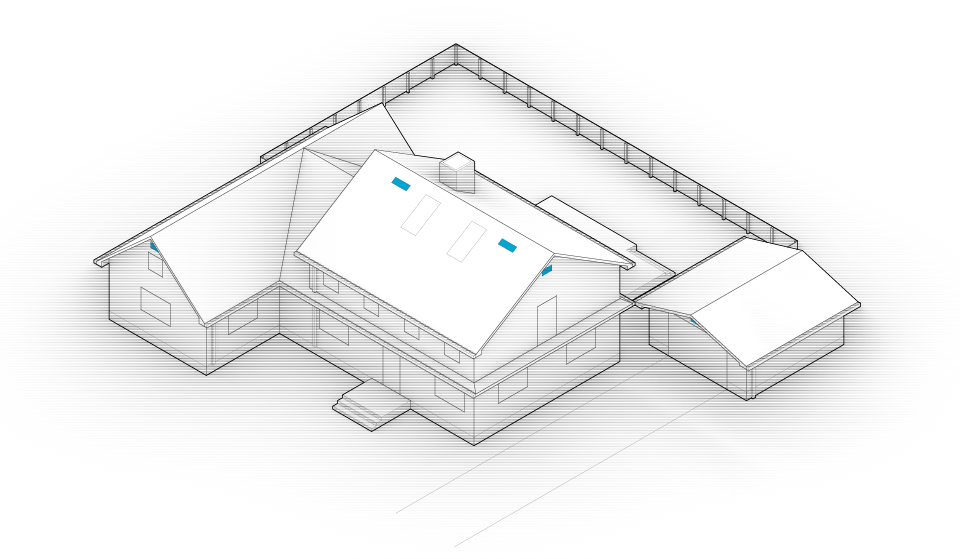
Identify the Vents
Multiple types of vents exist including:
- Attic and ventilated cathedral ceilings vents (e.g. ridge, soffit, and gable-end vents)
- Crawlspaces vents
- Heating, ventilation, and air conditioning (HVAC) systems (e.g. through-roof vents, wall louvers)
Use Non-combustible Materials
Install non-combustible materials for all vents and vent flashing (metal preferred).
Install Screens
If existing vent openings do not have screens or if the screen openings are larger than 1/4-inch, install corrosive-resistant, metal mesh screens with a maximum opening of 1/8 inch (3.2 mm) at all vent openings.
Attic and Soffit Vents are Vulnerable
Attic and soffit vents should be baffled to prevent ember intrusion. A metal mesh only reduces the risk of intrusion.
Install Shutters
Install shutters over gable-end vents, soffit vents, crawlspace vents, and wall louvers.
If the existing wall or soffit is combustible, shutters may not be effective. In this case, consider upgrading the walls or soffits with non-combustible material.
Sources:
Wildfire Research Fact Sheet – Roofing Materials (NFPA, 2017)
Fact Sheet No. 8 – Vents (FEMA, 2008)
P-737 Home Builder’s Guide to Construction in Wildfire Zones (FEMA, 2008)
Building and Living in the WUI (VCoFD, 2019)
Home Survival in Wildfire-Prone Areas: Building Materials and Design Considerations (UCANR, 2010)
Eaves, Overhangs, Soffit
The under-eave area is an exposed and vulnerable feature to windborne embers, direct flames, and radiant heat. They are a few easy steps that can help reduce the risk of ignition in this area by using noncombustible materials and retrofitting open eaves.
RELATIVE COST AND PRIORITY LEVEL OF HOME HARDENING FEATURES FOR FIRE-RESISTANCE
![]() |
![]() |
![]() |
![]() |
![]() |
![]() |
|
![]() |
||||||
![]() |
![]() |
![]() |
![]() |
|||
![]() |
Relative cost: Indicates the relative cost of upgrading the listed features to ember-resistant materials and design.
Priority level: Indicated the features most vulnerable to wildfires and embers. Keep in mind each situation is unique and may change your priority level.
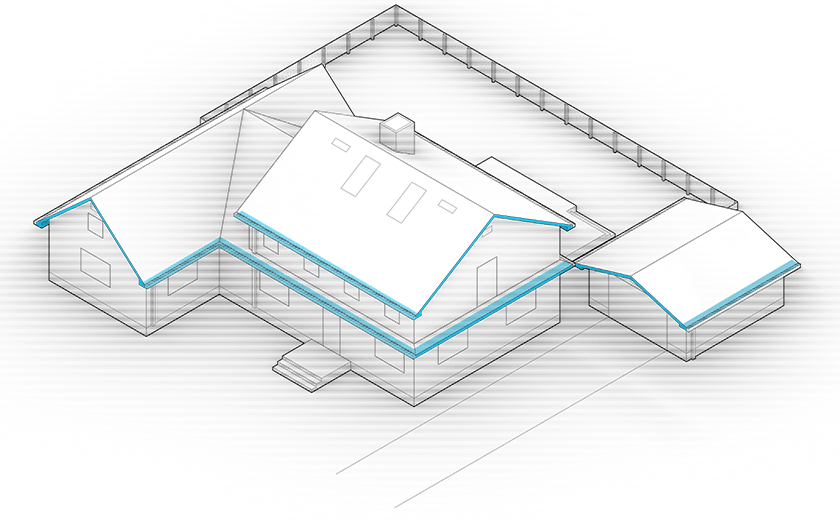
What are Overhangs and Soffits?
- Eaves are located at the down-slope edge of a sloped roof and serve as the transition between the roof and fascia/wall. An eave typically has a metal edge flashing and gutter that are attached to a wood fascia trim board.
- Overhangs are extensions of the roof beyond the exterior wall (i.e., the joists, rafters, or trusses and the decking they support cantilever past the wall). An overhang protects the upper portion of the wall that it is attached to from rainfall, and it also shades the windows under it from the sun.
- A soffit encloses the underside of sloped or flat-roof overhangs. Soffits are commonly constructed from fiber-cement panels, metal panels, stucco, vinyl panels, or wood sheathing. Metal panels, untreated wood panels, and vinyl panels are vulnerable to damage from wildfires. Metal panels conduct heat and can distort and allow passage of embers and hot gases. Untreated wood panels can ignite, and vinyl panels can melt and fall away.
Use Fire-resistant Materials
- Windborne embers, convective heat, and radiant heat can be trapped under overhangs and in the upper portion of exterior walls. Overhangs and walls can ignite if not constructed of noncombustible or fire-resistant materials.
- Consider designing the building without overhangs to avoid the fire-related problems associated with soffits. If you are considering overhangs:
-
- Enclose overhangs with soffits that have a minimum 1-hour fire-resistance rating
- Use flat, horizontal soffits instead of attaching the soffits to the sloped joists
-
- For the fascia, use noncombustible or fire-resistant materials (e.g., fire-retardant-treated lumber, fiber-cement board)
Check our “Upgrade” section to learn how to retrofit your eaves for fire-resistance!
Sources:
How To Prepare Your Home for Wildfire (NFPA)
Wildfire Research Fact Sheet – Under-eave construction (NFPA, 2017)
P-737 Home Builder’s Guide to Construction in Wildfire Zones (FEMA, 2008)
Building and Living in the WUI (VCoFD, 2019)
Home Survival in Wildfire-Prone Areas: Building Materials and Design Considerations (UCANR, 2010)
Walls, Sidings, Coatings
Exterior walls are susceptible to direct flames, conductive heat, and radiant heat. Flames and heat can ignite combustible wall coverings such as solid wood and wood composite. Vinyl and plastic products can deform and slough off when exposed to flame and heat. When exterior walls ignite, the fire can spread to other components of the building such as the roof, soffit, windows, and doors, resulting in substantial damage to or total loss of the building. Windborne embers and firebrands are common sources of ignition and can become trapped in cracks in walls, window openings, and door trim boards.
RELATIVE COST AND PRIORITY LEVEL OF HOME HARDENING FEATURES FOR FIRE-RESISTANCE
![]() |
![]() |
![]() |
![]() |
![]() |
![]() |
|
![]() |
||||||
![]() |
![]() |
![]() |
![]() |
|||
![]() |
Relative cost: Indicates the relative cost of upgrading the listed features to ember-resistant materials and design.
Priority level: Indicated the features most vulnerable to wildfires and embers. Keep in mind each situation is unique and may change your priority level.
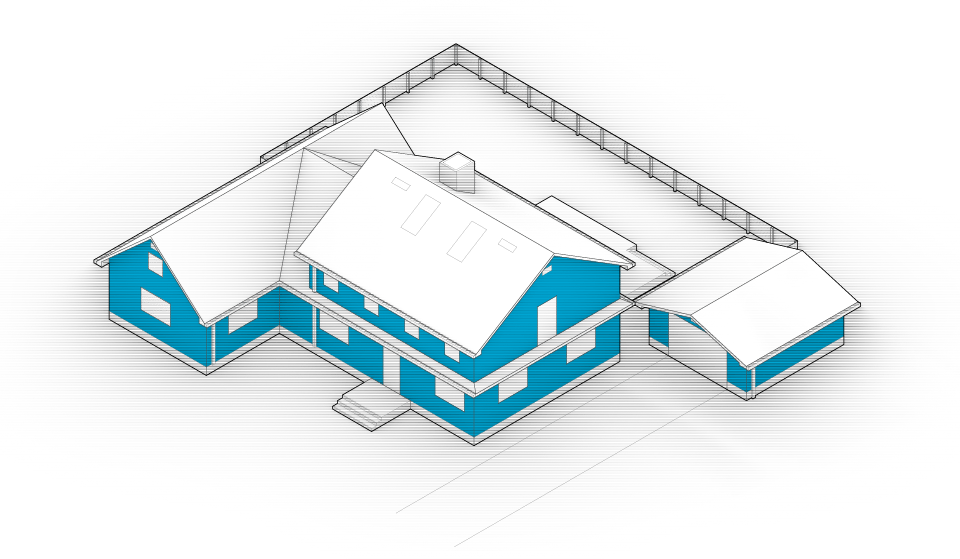
Recommended Materials
- Concrete
- Fiber-cement panels
- Pressure impregnated fire-retardant treated wood and panels
- Traditional three-coat stucco
- Masonry
- Metals (steel)
NOT Recommended
- Non pressure impregnated fire-retardant treated wood siding or panels
- Vinyl siding (will deform and fall off the wall at relatively low radiant heat or flame exposures)
- Metal siding susceptible to warping (aluminum)
- Exterior insulation finish systems (EIFS)
If you have a combustible siding and are unable to replace it in totality, target smaller areas that are vulnerable such as the 6-inch at the base of the siding and the roof-to-wall area. Creating a 6-inch noncombustible area at the base of the siding will minimize the chance that the siding will ignite from embers at the ground level or direct flame contact.
About Fire-retardant Coatings
Intumescent coatings, often referred to as intumescent paint, are used in buildings as a passive fire resistance measure. Usually, they have been developed for interior use are sometimes suggested for use in exterior applications, either applied as a primer or topcoat, on products such as siding.
While these products may work well in interior applications, they tend to lose effectiveness when used in exterior locations. The use of coatings as fire retardants should be avoided in exterior exposures until adequate information regarding performance after weathering has been demonstrated.
Sources:
How To Prepare Your Home for Wildfire (NFPA)
Wildfire Research Fact Sheet – Coatings (NFPA, 2017)
Fact Sheet No. 7: Exterior Walls (FEMA, 2008)
P-737 Home Builder’s Guide to Construction in Wildfire Zones (FEMA, 2008)
Building and Living in the WUI (VCoFD, 2019)
Home Survival in Wildfire-Prone Areas: Building Materials and Design Considerations (UCANR, 2010)
Windows, Sliding Glass Doors, Skylights
Windows, sliding glass doors, and skylights are key structure components to prevent ignition of the interior of your home because of intrusion of windborne embers, hot gases and radiant heat. You can reduce your ignition risk by following these recommendations for new constructions:
RELATIVE COST AND PRIORITY LEVEL OF HOME HARDENING FEATURES FOR FIRE-RESISTANCE
![]() |
![]() |
![]() |
![]() |
![]() |
![]() |
|
![]() |
||||||
![]() |
![]() |
![]() |
![]() |
|||
![]() |
Relative cost: Indicates the relative cost of upgrading the listed features to ember-resistant materials and design.
Priority level: Indicated the features most vulnerable to wildfires and embers. Keep in mind each situation is unique and may change your priority level.
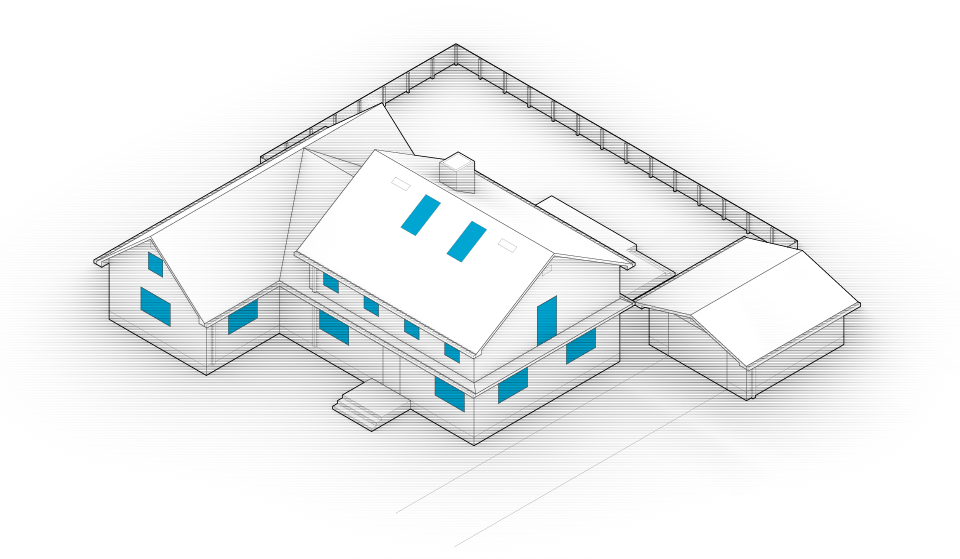
Recommended Glazing
- Tempered glass is more resistant to heat and flames than laminated glass or annealed glass. The resistance of tempered glass can be enhanced with a low-e coating or a proprietary reflective coating.
- Glass with a low-e coating provides a higher level of resistance to radiant heat than other types of glazing because the coating reflects radiant heat, reducing the probability that the heat will be able to enter the building.
- Proprietary fiberglass-reinforced translucent glazing. This product is available for skylights and walls. The skylight material has a Class A rating.
- Insulated glazing unit (IGU). An IGU consists of two or three panes of glass that are separated by a sealed air space. Double-paned annealed units last about 10 minutes in a wildfire, twice as long as single-paned windows.
Not Recommended
- Annealed glass
- Ceramic glass
- Plastic glazing (often used in skylights)
Use Non-combustible Materials for Frame
To avoid window failure, frames should be constructed only of metal or metal-clad wood. Wooden and plastic frames should not be used.
Install Exterior Window Shutters
Exterior window shutters can provide protection for windows and sliding glass doors in a wildfire. Solid metal shutters are unlikely to ignite or melt and are therefore recommended over wooden or plastic shutters.
Skylights
- Low-Slope Roof
Vegetative debris can accumulate more on a low-slope roof, increasing the risk for a flat glass skylight to break as typical flame temperature from wind-blown ember ignited debris is high enough to break tempered glass usually used for the outer pane. For this reason, dome skylights are preferred on slow-slope roofs as long as they meet the requirements of Chapter 7A. - Steep-Slope Roof
Flat skylights are less vulnerable on a steep-slope roof because vegetative debris are less likely to accumulate. Flat skylights on steep-slope roofs are however still vulnerable to extended radiant heat exposure from nearby vegetation and combustible materials. Newer skylights usually feature dual-pane systems similar to windows with a tempered glass outer pane. This multi-pane design reduces the likelihood of failure of these skylights.
Sources:
How To Prepare Your Home for Wildfire (NFPA)
Wildfire Research Fact Sheet – Skylights (NFPA, 2017)
P-737 Home Builder’s Guide to Construction in Wildfire Zones (FEMA, 2008)
Building and Living in the WUI (VCoFD, 2019)
Home Survival in Wildfire-Prone Areas: Building Materials and Design Considerations (UCANR, 2010)
Doors
The design and construction of exterior doors, including garage doors, on buildings in wildfire zones is critical to prevent ignition from ember intrusion or radiant heat. Exterior doors are subject to the same types of exposure as exterior walls but are usually much thinner and less resistant, making them an important component in your home hardening plan.
RELATIVE COST AND PRIORITY LEVEL OF HOME HARDENING FEATURES FOR FIRE-RESISTANCE
![]() |
![]() |
![]() |
![]() |
![]() |
![]() |
|
![]() |
||||||
![]() |
![]() |
![]() |
![]() |
|||
![]() |
Relative cost: Indicates the relative cost of upgrading the listed features to ember-resistant materials and design.
Priority level: Indicated the features most vulnerable to wildfires and embers. Keep in mind each situation is unique and may change your priority level.
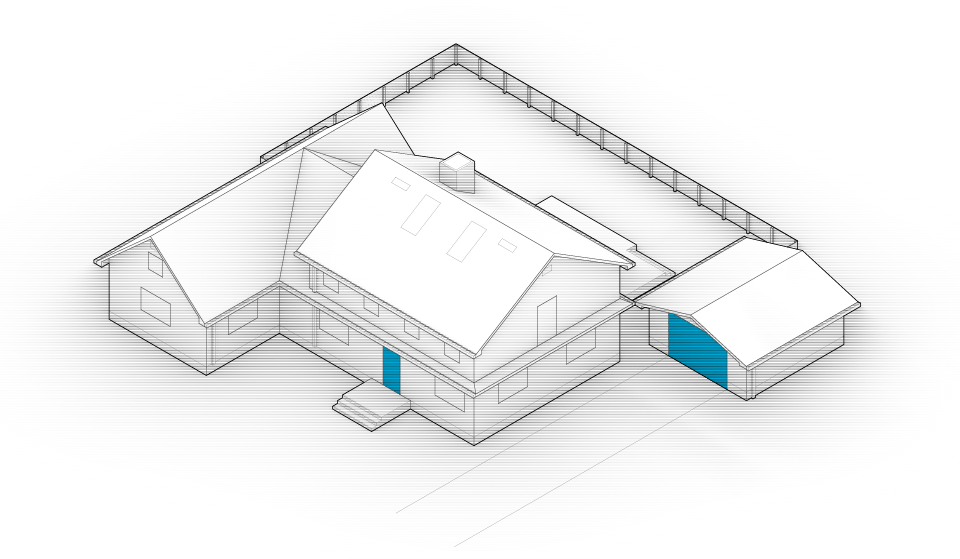
Exterior Doors
- Install a fire-rated door and frame. Doors with a solid, noncombustible mineral core are classified as fire-rated doors. Exterior fire-rated doors are available with a rating of 1½ hour or 3/4 hour.
- For door glass vision panels and glass sliding doors, follow recommendations in Windows & Skylights.
Weatherstripping
Install adjustable weatherstripping on the interior side of the door frame and specify and install an automatic door bottom or threshold weatherstripping. The weatherstripping and door bottom should be tested in accordance with UL Standard 10C. Weatherstripping is relatively inexpensive.
Garage Doors
- Install insulated, metal garage doors.
- Install weatherstripping that has been tested in accordance with UL Standard 10C around the entire garage door.
For exterior trim that covers the opening between the door frame and exterior wall. Install noncombustible or fire-resistant material such as fire-retardant-treated wood or fiber-cement board.
Sources:
How To Prepare Your Home for Wildfire (NFPA)
Fact Sheet No. 11: Exterior Doors (FEMA, 2008)
P-737 Home Builder’s Guide to Construction in Wildfire Zones (FEMA, 2008)
Building and Living in the WUI (VCoFD, 2019)
Home Survival in Wildfire-Prone Areas: Building Materials and Design Considerations (UCANR, 2010)
Fences
Landscape fencing and walls that are attached to or near buildings in wildfire zones can represent a high ignition risk by spreading flames or radiant heat from one building to another. The common wooden post-and-board fence can become fuel for a wildfire, especially when the fence is old and weather-beaten. It can also collect embers and firebrands in a wildfire and act as a horizontal ladder fuel by allowing the fire to travel along the fence. Masonry, concrete, stone, metal, and hardwood landscape fences and walls are effective ignition-resistant materials. The most common product meeting the ignition-resistant material requirements is exterior-rated fire-retardant treated wood 4 by 4-inch (or larger).
RELATIVE COST AND PRIORITY LEVEL OF HOME HARDENING FEATURES FOR FIRE-RESISTANCE
![]() |
![]() |
![]() |
![]() |
![]() |
![]() |
|
![]() |
||||||
![]() |
![]() |
![]() |
![]() |
|||
![]() |
Relative cost: Indicates the relative cost of upgrading the listed features to ember-resistant materials and design.
Priority level: Indicated the features most vulnerable to wildfires and embers. Keep in mind each situation is unique and may change your priority level.
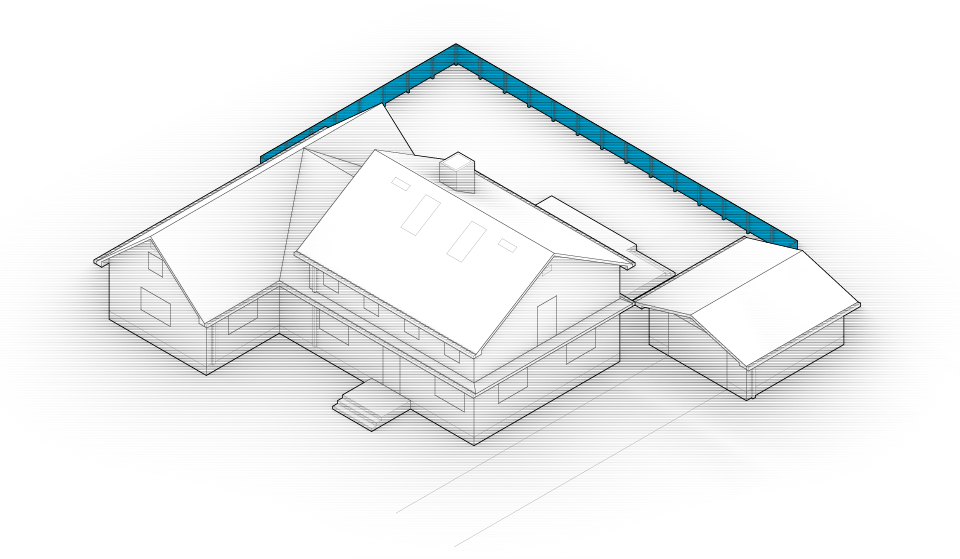
Fire resistance of common materials used for landscape fencing
Wood
Fences that are constructed of wood or have wooden components are combustible and therefore provide no fire resistance. A wood frame with steel mesh infill is an option that would minimize the possibility for an ember ignition; however, if vegetation is allowed to grow on the mesh infill, this advantage will be negated.
Plastic
Plastic fences are more fire-resistant, more durable, and often stronger than wooden fences, but plastic fences can melt in a wildfire from temperatures that are below the maximum a wildfire can generate.
Metal
Metal fences are more fire-resistant than plastic fences. Wire fences such as barbed wire, hog wire, and chain link have little or no effect on fire passage. However, if combustible materials have accumulated in or around the fence, it can act as a horizontal ladder fuel by allowing the fire to travel along the fence.
Concrete, stone, or masonry
Concrete, stone, and masonry fences and walls are noncombustible and can act as a barrier to a wildfire by deflecting flames away from a building.
Key Considerations for Increased Fire Safety
- Avoid attaching fences and walls constructed of combustible materials to a building.
- For fences and walls that are attached to a building, ensure that all combustible components are at least 5 feet from the building to prevent heat and flames from igniting the building. A common technique is to use a metal gate with one side attached to the combustible fence and the other to the building.
- A fence design that allows for greater air flow, such as a single panel lattice fence, makes it more difficult for wind-blown embers to accumulate at the horizontal to vertical intersection. For this reason, privacy fences with all planks on one side are the most vulnerable to ignition.
- A fence with lattice applied to both sides of the support posts should be avoided due to fire growth and lateral flame spread.
- Avoid combustible mulch and vegetation within at least 2’ of combustible fencing.
Sources:
How To Prepare Your Home for Wildfire (NFPA)
Wildfire Research Fact Sheet – Fencing (NFPA, 2017)
Fact Sheet No. 14 – Landscape Fences and Walls (FEMA, 2008)
P-737 Home Builder’s Guide to Construction in Wildfire Zones (FEMA, 2008)
Building and Living in the WUI (VCoFD, 2019)
Home Survival in Wildfire-Prone Areas: Building Materials and Design Considerations (UCANR, 2010)
Decks
Decks are important features because they are usually attached to a home and are next to a window or sliding glass access door. Consider the construction material used to build the deck, patio or porch, along with the furniture and other items stored beneath it. This area is part of your defensible space so also consider the vegetation leading up to the deck.
RELATIVE COST AND PRIORITY LEVEL OF HOME HARDENING FEATURES FOR FIRE-RESISTANCE
![]() |
![]() |
![]() |
![]() |
![]() |
![]() |
|
![]() |
||||||
![]() |
![]() |
![]() |
![]() |
|||
![]() |
Relative cost: Indicates the relative cost of upgrading the listed features to ember-resistant materials and design.
Priority level: Indicated the features most vulnerable to wildfires and embers. Keep in mind each situation is unique and may change your priority level.
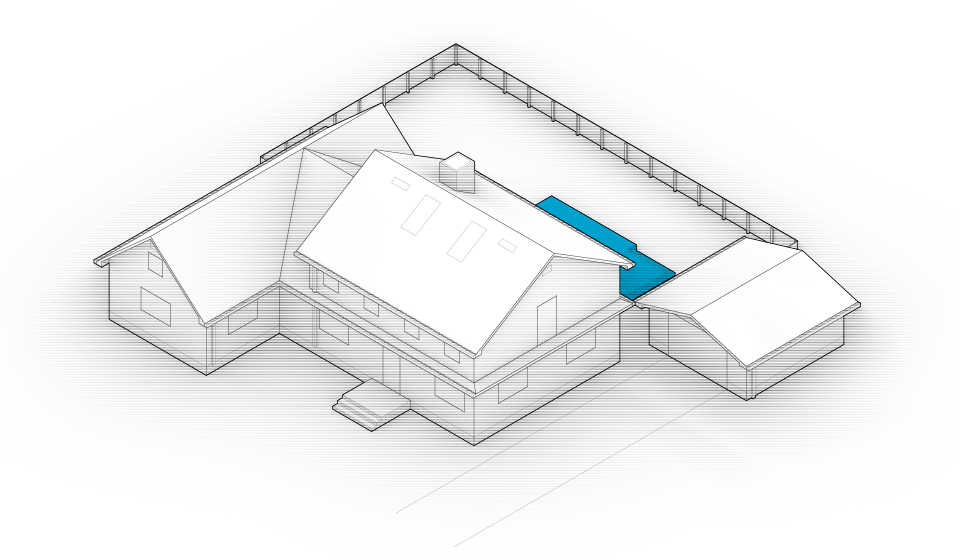
Plastic and Wood-plastic are also Combustible
It is common knowledge that wood deck boards are combustible. There is sometimes a misunderstanding regarding the combustibility of plastic and wood-plastic composite decking products—these decking products are also combustible.
Recommended Spacing
Untreated wood and wood treated with fire-retardant, as well as plastic and wood-plastic composite products are all combustible and therefore vulnerable to ember and other wildfire exposures. However, the deck can be designed to minimize exposure to embers:
- Increase the gap between deck boards from 1/8 inch to 1/4 inch.
- Increase joist spacing from 16 inches to 24 inches. Apply a foil-faced self-adhering adhesive flashing tape (foil-faced bitumen tape) on the top of each joist. Foil tape should extend down each side of the joist 2-3 inches.
Sources:
How To Prepare Your Home for Wildfire (NFPA)
Wildfire Research Fact Sheet – Decks (NFPA, 2017)
Wildfire Research Fact Sheet – Fire spread on ember-ignited decks (NFPA, 2017)
Fact Sheet No. 13 – Decks and Other Attached Structures (FEMA, 2008)
P-737 Home Builder’s Guide to Construction in Wildfire Zones (FEMA, 2008)
Building and Living in the WUI (VCoFD, 2019)
Home Survival in Wildfire-Prone Areas: Building Materials and Design Considerations (UCANR, 2010)
Defensible Systems
Defensive actions can potentially help your home survive a wildfire. These actions are in addition to creating and maintaining defensible space on your property and selection of appropriate building materials listed on this website.
RELATIVE COST AND PRIORITY LEVEL OF HOME HARDENING FEATURES FOR FIRE-RESISTANCE
![]() |
![]() |
![]() |
![]() |
![]() |
![]() |
|
![]() |
||||||
![]() |
![]() |
![]() |
![]() |
|||
![]() |
Relative cost: Indicates the relative cost of upgrading the listed features to ember-resistant materials and design.
Priority level: Indicated the features most vulnerable to wildfires and embers. Keep in mind each situation is unique and may change your priority level.
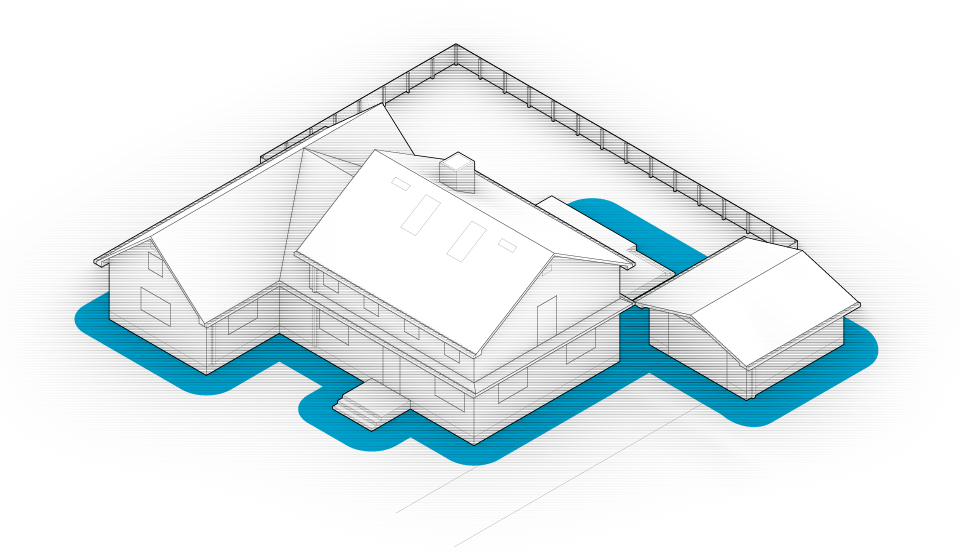
Exterior Water Spray Systems
An exterior water spray system can be roof- or ground-mounted. The objective of the sprinklers is to limit the spread of the fire to the home and/or extinguish wind-blown embers before they reach the building being protected. It is important to understand that the effectiveness of an external sprinkler system has not been completely evaluated.
If you are considering an external sprinkler system, check with your local fire department. They may have plans, and other suggestions. In order to maximize the effectiveness of exterior sprinklers, they should be on a stand-alone, independent water system (i.e., tank, pool or lake) and should be attached to a pressurized delivery system or use a generator for needed pumps.
Gel Coating
Gels are water absorbent polymers that can be applied to a building component to provide temporary protection from radiant heat or flames. You may have heard of these products being applied to homes when a wildfire is threatening. Once applied, the absorbed water starts to evaporate, whether or not the wildfire actually arrives, and therefore the time that a gel coating is effective is limited. The effective time is on the order of hours. It is not warranted to rely on a coating in lieu of managing vegetation or improving building materials and design.
Given the potential issues regarding performance, it is recommended that the use of defensive actions be a supplement to, and not a replacement for, already proven mitigation strategies, such as the reduction of potential fuels throughout the home ignition zones, along with removal of roof and gutter debris, and use of noncombustible and fire/ember-ignition resistant building materials and installation design details.
Sources:
How To Prepare Your Home for Wildfire (NFPA)
Wildfire Research Fact Sheet – Exterior Sprinklers Systems (NFPA, 2017)
Wildfire Research Fact Sheet – Fire spread on ember-ignited decks (NFPA, 2017)
Fact Sheet No. 15 – Fire Sprinklers (FEMA, 2008)
Fact Sheet No. 16 – Utilities and Exterior Equipment (FEMA, 2008)
P-737 Home Builder’s Guide to Construction in Wildfire Zones (FEMA, 2008)
Building and Living in the WUI (VCoFD, 2019)
Home Survival in Wildfire-Prone Areas: Building Materials and Design Considerations (UCANR, 2010)
CALFIRE provides a list of Wildland Urban Interface (WUI) Approved Products.
Visit their website and search for “8180 – Non-Wood Roof Covering / Assemblies for Wildland Urban Interface (WUI)”.